Key Takeaways:
- Lead time is the total time from the initiation to the completion of a production process.
- Reducing lead time is crucial for improving responsiveness and customer satisfaction.
- Effective lead time management requires optimizing each stage of the production process and eliminating bottlenecks.
As manufacturers embrace digital technology and control, consumers are doing the same. Whether that consumer is the product user or the wholesaler, digital technology and IoT have changed the expectations they put on the manufacturer.
Customers expect products to be simple and easy to order, as well as fast to deliver. Expectations are higher than ever, and if manufacturers want to compete, they'll need to continue meeting customer demand and exceeding what their customers are asking for.
One metric used to understand a company’s ability to meet customer demand and drive customer happiness is Lead Time. Manufacturers use lead time to benchmark efficiency and identify areas for process improvement to reduce the time required to deliver finished parts or goods to customers.
Let's take a closer look at lead time and discuss how managers can focus on getting finished products into customers' hands faster than ever before.
What is Manufacturing Lead Time?
Lead time is the total time from when a customer places an order until it’s delivered.
Lead time includes the administrative, management, procurement, inventory, and logistics functions.
This provides an overall measure of how efficient an operation is at taking and fulfilling orders.
Types of Lead Time
Many types of lead time can be measured in manufacturing. By separating them into categories, managers and technicians can drive process improvements to reduce lead time for each type.
Types of manufacturing lead time include:
Customer Lead Time
This lead time is the one most understood by those outside the company, like customers, retailers, and suppliers. Customer lead time is the total time between when the order is placed and when it’s delivered.
Material Lead Time
Material lead time is the total time between recognizing a need for material and when the material arrives. Many manufacturers have some safety stock, so the realization isn’t necessarily when the material reaches zero. It can be calculated from an established minimum reorder point as well.
This lead time may include several variables like manufacturing time at the vendor, shipping time, and more. Supply chain planners use material lead time to meet production schedules and reduce wait time for inbound stock.
Production Lead Time
Production lead time begins when the material for an order has arrived and is scheduled through the entire production process. It assumes that all necessary materials are in stock and machines are available for production.
Plug-and-play Machine Connectivity
While external factors may impact other types of lead time, production lead time is internally managed. It can be controlled and measured accurately by optimizing labor, reducing waste, controlling machine downtime, and optimizing processes on the shop floor.
WIP Lead Time
Some companies manage WIP lead time to further drill down into the production process and identify areas for improvement. WIP time is the time material takes to move through various sub-processes within manufacturing, and the total WIP lead time equals production lead time.
Cumulative Lead Time
Cumulative lead time is the total time of all other lead time categories. It allows managers to look at the macro and micro KPIs for lead time and identify areas for improvement in the sales and production processes.
How Do You Calculate Lead time?
The calculation for lead time is simple: the date of delivery minus the date when the order was placed.
LT = OD – OR
- LT = Lead Time
- OD = Order Delivered
- OR = Order Received
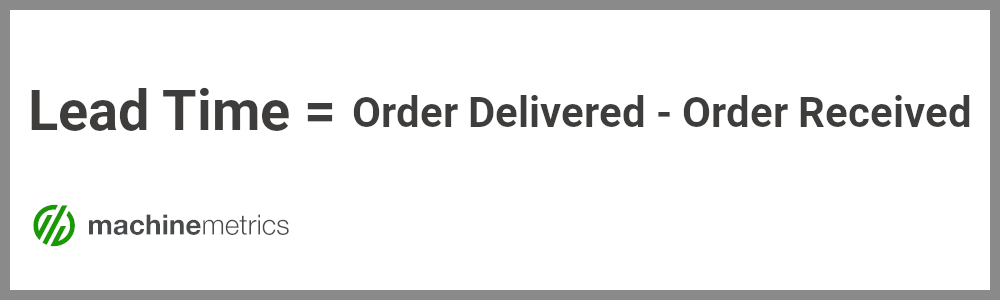
Lead time is usually expressed in days, providing a rational format for the manufacturer and customer to understand during communication. On the other hand, cycle time is generally expressed in seconds, minutes, or hours.
Why is it Important to Reduce Manufacturing Lead Time?
Lead time impacts the entire manufacturing process, and there are many benefits to reducing it. These reasons include the following:
Greater Customer Satisfaction
Today's consumers are more sophisticated and informed, and they have greater expectations of suppliers. Reduced lead time means faster order fulfillment, which can result in higher customer satisfaction, repeat orders, and improved brand awareness.
Lower Manufacturing Costs
When manufacturing processes are optimized, fewer labor and equipment resources are required to produce the same amount of goods. This optimization results in lower manufacturing costs.
Lower Holding Costs
Inventory management teams must constantly balance warehouse space, indirect labor, and logistics to meet production demand. If lead times are reduced, material flows through manufacturing more rapidly, reducing holding costs.
Reduced Waste
Waste can occur in the form of labor (such as wait time) or spoilage (in industries where material may need to be thrown out). It can also occur when materials are expedited, risking too much of one component or creating dead stock. Reduced lead times mean less waste in many areas.
Better Demand Planning
In fast-paced industries where demand changes quickly or seasonally, reduced lead times help planners manage demand more accurately. Planners can forecast in the near and long term to ensure capacity is available to meet demand while also having time to react to disruption.
Factors That Affect Manufacturing Lead Time
Manufacturing is a complex system of inputs. A change in any one of these inputs can disrupt the entire manufacturing process and increase lead time. Factors that can impact manufacturing lead time include:
Disruption
Disruption may be as simple as a missed cargo ship or broken trailer axle. It may also result from natural disasters like hurricanes, floods, or other events. These and other similar events can increase lead times.
Raw Material Shortages
There was a time not long ago when few companies worried about material shortages. But events like COVID-19, trade wars, and logistics bottlenecks have resulted in raw material shortages and increased lead times.
Labor Shortages
The labor market has tightened in recent years, highlighting the need for more process automation. When labor is unavailable and manufacturing processes aren’t optimized, jobs may be idle at critical times.
Manual Quality Control and Inspection
The lead time of finished goods can increase when quality control processes are manual. The more resources added for inspection, the greater the lead time. Without automated quality measurement using sensors and advanced analytics, quality becomes a trade-off between longer lead times and higher waste.
Manual Production Monitoring
When companies manually track production, they risk overproducing or underproducing goods. Like quality inspection, manual production monitoring is a trade-off. Greater detail increases cost and labor, while less monitoring may let some orders finish short while others overproduce.
Plug-and-play Machine Connectivity
Broken Processes
Broken processes occur when a piece of the production system doesn't work as it was designed to. Workarounds, missed communication, and unsanctioned tasks increase the time required to produce finished goods. In manual systems, a broken process may continue for years, reducing overall equipment effectiveness, driving up cost, and dramatically increasing lead time.
Human Error
Any manual part of the production process — inventory management, planning, procurement, quality, or shipping — has the potential for human error. Errors can create machinery downtime, increase process time, trigger unnecessary processes, and increase lead time cumulatively. Some errors are so great they can increase manufacturing lead time independently.
How Do You Reduce Lead Time?
Lead times are quoted by the vendors producing materials for manufacturers. Manufacturers, in turn, quote lead times to their customers for finished goods or parts.
Lead times can allow manufacturers to improve their processes, optimize logistics, and streamline scheduling and forecasting. By reducing total lead time, manufacturers can better meet customer expectations and develop a key competitive advantage.
Here are a few ways to reduce lead time:
Improve Management and Inventory Control
Stockouts occur when materials or parts are unavailable for required orders. This shortage can lead to a ripple effect where other production must be moved, pulled forward, or delayed as the manufacturer rushes to deal with the problem.
The best way to reduce stockouts is by automating the inventory process. Manual inventory management in the age of IoT and digital technology is highly inefficient. By automating the inventory process, inventory is optimized to meet order demand.
But stockouts are only part of the problem. Human error in manual inventory transactions reduces visibility on the production floor. These errors may impact production, cause unnecessary expediting, and affect WIP needed for production.
Inventory management software is an excellent first step in the optimization process needed to reduce stockouts and drive inventory optimization. Linking this software with a machine data platform allows for an accurate perpetual inventory management system tied to other real-time monitoring to ensure that production always has what is needed and knows when replenishment will occur.
Audit and Manage Vendor Relations
It’s not uncommon for manufacturers to utilize several vendors for the same material, which may be considered interchangeable or backup. But in today’s business environment, disruption is the norm. Auditing and combining vendors can help reduce variable lead times due to vendor performance.
Going one step further, if cost-effective, there is an opportunity to in-source work that has historically been outsourced to other companies.
Eliminate Unnecessary Processes
Manufacturing is a complex process. With multiple variables such as OEM, machine type, operator training, product type, and more, processes are more intricate than ever. But many companies still contain a high degree of manual management and process intervention.
While reducing lead times in the above examples can be accomplished through automating tasks and processes, there is no better way to reduce manufacturing lead time than by eliminating unnecessary processes that are slowing down the time it takes to produce and supply finished products to customers.
Using Production Data to Drive Down Lead Times
With a production monitoring platform like MachineMetrics, companies can connect factory assets and monitor production down to the machine and spindle level. Many manual tasks and processes can be automated or semi-automated to drive greater operator performance and machine utilization.
MachineMetrics also provides real-time actionable insights based on production data. This allows managers to identify trends quickly, pinpoint areas needing intervention, and craft strategies for process improvement. Ultimately, they can drive incredible gains in efficiency.
A machine data platform can eliminate unnecessary processes such as:
Machine data can also enable automated workflows to automate low-value activities. This enables manufacturers to develop advanced production floor strategies (such as predictive maintenance) to lower costs and respond to machines’ needs based on actual use and wear.
By replacing preventive maintenance with predictive maintenance, replacing manual inventory control with optimized perpetual inventory, and automating machines across the factory floor, the remaining processes drive higher efficiency and reduce lead time significantly.
MachineMetrics offers a best-in-breed machine data platform that leverages your equipment’s real-time data to improve existing processes, eliminate unnecessary ones, and significantly reduce lead time to meet today’s demanding customer expectations.
Want to See the Platform in Action?
Comments